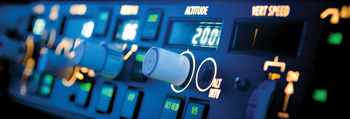
Delivering airline pilot training to mitigate the risk of loss of control–in flight (LOC-I) partly depends on technical innovations that mesh precisely with new regulations, standards and expert guidance (ASW, 7/13, p. 27, and 8/13, p. 34). Behind-the-scenes details provide evidence of progress to date on these innovations, as seen by some of the international specialists involved, and offer insights on what constitutes acceptable results from key hardware-software solutions, and their limitations.
For many years, the effectiveness of existing engineered solutions for accident prevention was the subject of wide-ranging debate, some specialists told the 8th International Flight Crew Training Conference, held in September 2013 in London by the Royal Aeronautical Society. Overall, the specialists voiced confidence in current or imminent technical capability to support this training.
Michael Varney, a captain and senior director, flight crew training, Airbus, told the conference, “The fact is that over decades, we have looked at these sorts of statistics [for LOC-I, controlled flight into terrain, ground collisions and runway excursions] and fixed the problems on an engineering basis instead of looking behind what the root causes of the problems are. … As we design-out known problems and we improve the reliability of our already very reliable system, failures are much less likely. Nevertheless, when we put human beings in the cockpit, there are all sorts of potential, possible interactions and some things that we cannot predict by design. … We can create, with help from our simulator manufacturers, a really immersive environment where the pilots feel 90 percent that they’re really in the airplane — and that they really have to deal with the situation.”
Technical Solutions
Analyses of technological possibilities have clarified the research and development priorities and the benefit-to-cost ratios, said Jeff Schroeder, chief scientific and technical adviser, flight simulation systems, U.S. Federal Aviation Administration. He spoke as chairman of the Research and Technology Group of the International Committee for Aviation Training in Extended Envelopes. The committee, a four-year initiative of the Royal Aeronautical Society, disbanded in late 2013.
There’s no longer a question that conducting high-altitude stall prevention training in flight simulation training devices (FSTDs) offers the highest benefit-to-cost ratio for operators, he said. This has been the flight regime where stalls in transport category airplanes have happened recently, and where recovery is the most challenging. Practice applying the most effective response — based on first reducing angle-of-attack — instills confidence and reinforces the current procedure, he said.
“Because of the roll damping, the ensuing recovery to get back to safe flight can expose some deficiencies with a rare number of pilots,” Schroeder said. “In the United States, we have to do full-stall training and, based upon some recent experience, it looks like that appears to be feasible in simulators. … No airplane stalls the same way twice, and … our proposed modeling specification [has] a component of randomness that goes into the models so that it’s consistent with the variation [flight crews] will see in the airplane.”
The group first sought expert opinion — often from test pilots highly experienced in stalling the same aircraft types — to rate the realism created by new software algorithms installed in an FSTD, then conducted technology demonstrations, evaluations and experiments. In November 2010, for example, the group assessed a new representative stall model algorithm that, unlike typical algorithms, was not based on flight test data (see “Configurable Model”).
“[In 2013,] we did an experiment that involved looking at four different types of stall models, one being an unmodified [algorithm] that is delivered with the simulator now,” Schroeder said. “Ten test pilots — nine of whom had stalled an actual [Boeing] 737 airplane, one over 500 times — evaluated [these] so we had a lot of confidence [in] the opinions that we were getting on the model fidelity. In another part of the experiment, I had 40 747 line pilots come in and get trained on the various stall models, and then we checked them after they had trained to proficiency in recovering from several [stall] scenarios on the type-specific stall model developed by The Boeing Co.”
False Success
Configurable Model
Wind tunnel experiments for modeling high-altitude stall have proven to be equally or more important than relying on flight test data to create a new configurable simulation, according to one conference presentation. “What we’re trying to do, working with the U.S. Federal Aviation Administration, is to postulate the potential of configuration geometry types to simplify the stall model deployment,” said John Ralston, president of Bihrle Applied Research. “The reason for doing this is to try to minimize the amount of model-specific work that needs to be done in order to accomplish this. This also gives us an approach to [modeling] where we might not have available the original equipment manufacturer [flight test] data to support the stall model development.”
The wind tunnel experiments aimed to develop a stall model configurable for most of the aircraft that have a “swept low wing, low tail, underwing-engine configuration,” he said. “We wanted to identify the requisite model architecture that would capture the stall features [and type-specific baseline data,] configuration-representative reductions in the static and dynamic stability in both longitudinal and lateral directional axes; reductions in control effectiveness; [enhanced buffet;] and an asymmetric behavior that also characterizes rolloff,” Ralston said. This is not a generic model but rather a model that can be adjusted in real time inside an engineering simulator based on a subject matter expert’s recommendations.
Nonlinear characteristics such as stable-versus-unstable roll damping have been relatively difficult to identify from flight test data but can be readily identified in the wind tunnel; nevertheless, wind tunnel test data also have limitations, he said.
An enhanced stall model demonstration of the technology, using a Sim Industries Boeing 737-800 device, was conducted for the Research and Technology Group of the Royal Aeronautical Society’s committee, said Dave Gingras, vice president, Bihrle Applied Research. The enhanced modeling was implemented by transitions between existing and new algorithms as necessary, and running the blended simulation externally on modern computer hardware so that the relatively low computing power of legacy flight simulation training devices would not be an issue.
Mismatching a technology to a training element may create the risk of a negative transfer of training, he said. Another committee concern was that a pilot might attempt to recover from a high-altitude stall when the aircraft actually was not stalled. Such a scenario might be prompted inadvertently by activation of the stick shaker during moderate turbulence.
“The pilot misconstrues that as a stall condition and then places the nose down, executes a full recovery in the sparse air [but then gets] into pilot-induced oscillations in the recovery, varying in [g loads, the positive or negative multipliers of normal gravitational acceleration],” Schroeder said. “The worst case that we saw went between 0.2 g and 2.2 g. If you’re not paying attention to the barber pole [minimum-speed amber and red bands on a Boeing speed tape, for example] going up and down and oscillating — your angle-of-attack is changing, your lift is changing and your load factor is changing — you might think this was a pretty good recovery. And it wasn’t.”
Accurately simulating recovery from a full stall is one of the areas where simulation engineers still need to spend time, he said. Further work also is needed to improve the buffet realism so that buffeting progressively changes to reflect depth of entry into the stall region of the aerodynamic envelope; the feedback to instructors; the mathematical modeling of recovery; and the modeling of the effects of icing on stall.
“Roughly, we have about 50 different aircraft [variants] that we probably have to make models for … in the United States, across about 300 simulators in the air carriers,” he said. “Most of the [upset prevention, recognition and recovery training] can be done today, especially on the prevention side, with our existing tools. … By 2018, everybody in the United States that flies [Federal Aviation Regulations] Part 121 [air carrier] operations will have to comply.”
Enter the Matrix
A key factor in the group’s progress in closely aligning technical capabilities with the committee’s 176 training elements was a comprehensive training matrix (Table 1), said Dennis Crider, chief technical adviser, vehicle simulation, U.S. National Transportation Safety Board (NTSB). “The matrix contains training elements necessary for the pilots to [acquire] skills to recognize and recover from in-flight upsets,” he said. They also cover, for stall in icing conditions, the types of automation mismanagement, stalls-without-warning and aircraft nose-below-horizon scenarios commonly seen in NTSB accident data, he added.
Airline pilots have long needed to be trained on “what lies beyond the stick shaker,” Crider said. If this training is effective, the various cues to imminent stall and stall can be transformed — by qualified instructors using appropriate technology — from sources of confusion to familiar inputs that rapidly trigger the correct response.
The group also did an exhaustive fidelity-requirement analysis, deciding the specific level for every combination of device and training element. Each task was characterized as practical, academic or both, and separately assigned to mitigation levels within upset awareness; recognition and prevention; and/or recovery stages, said David Shikany, associate technical fellow, aerodynamics stability and control, flight simulation, The Boeing Co.
“We took each training task, and we looked at it from the point of view of the cues that were required,” Shikany said. “The awareness and the alerting cues were relevant to the control forces, the instruments and the audio cueing that is associated with [the all-attitude exposure] training task. The control forces and the motion cueing both play a role in the pilot’s ability to control the aircraft in order to be able to carry out the training task. And motion cueing has a major physiological effect in the all-attitude exposure training task. So we carried this out for all of the 176 tasks, and once we’d done that, we then felt that we could go back and link [each required cue] to the FSTDs.”
He cited the awareness level of training for high-altitude stall as an example. “There’s going to need to be a representative level of fidelity in the flight model — in the control forces in the cockpit, for example — to be able to meet the learning objective … to understand the relationship between high alpha [angle-of-attack] and increased induced drag,” Shikany said. A diagram produced by the group shows that the industry already has devices that meet that level of fidelity.
‘Genetic Code’
In parallel with the fidelity work, the group assigned a code to each detail of the capabilities of commonly used FSTDs, said Joris Field, training systems specialist, National Aerospace Laboratories Netherlands.
“[We took] all the fidelity requirements for the various features and essentially aligned them into a device,” Field said. “Unfortunately, the 176 tasks that are in that matrix resulted in over 40 unique ‘genetic codes.’ … [Instead of] standardizing down to seven devices, you would [have to] turn all those unique genetic codes into 40 different devices.” The solution in some cases was to “roll up” similar sets of codes into what he called “a common genetic code or set of fidelity requirements that could satisfy a number of the tasks” first by using today’s ICAO Type II, Type V and Type VII FSTDs.
“Then we found that we had to essentially come up with four new devices,” he said, describing how the group distilled the desirable leftover codes into a Type VII+ device, a g-awareness device, a spin device and a spatial disorientation device. “For the Type VII+ device, there were 18 [codes] primarily associated with training tasks related to the stall. … The Type VII+ device does require some additional enhancements to the flight model primarily for stall, control forces, flight control forces, stick pusher, motion buffet, environment, weather and the IOS [instructor operating station]. … One of the things we’ll have to be aware of [is that if] the training objectives change, those device requirements will have to change also. … Over three-quarters of the training in that matrix can be accomplished with today’s devices plus some enhancements. … There always will be a subset of those training objectives that will be required to be performed on the airplane due to psychological or physical effects.”
“How do we simulate all this?” asked Itash Samani, head of global FSTD regulations, CAE. “The level of the [current standard Type VII, a ‘Level D+’] device is our starting point [and] what is commonly out there.”
In the near future, the industry also can look forward to accurate representation of stall behavior in icing conditions with new Type VII models instead of today’s unrepresentative, artificial increases in aircraft weight and drag as a proxy. New models will include loss of lift; increasing drag; change in the stall angle-of-attack, which prevents normal stall warnings; changes in the pitching moment of the aircraft; and decreased control effectiveness, and changes in control forces, he said.