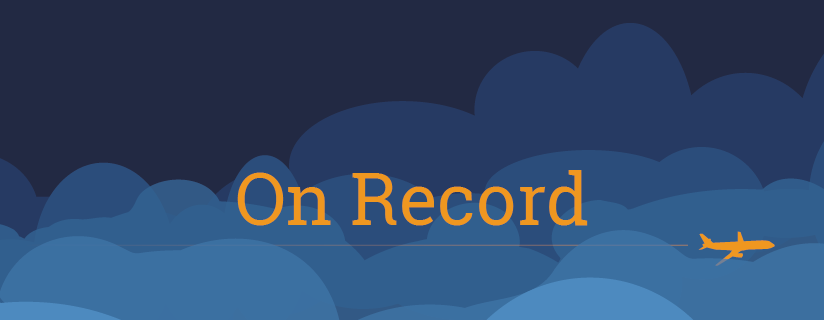
The following information provides an awareness of problems that might be avoided in the future. The information is based on final reports by official investigative authorities on aircraft accidents and incidents.
Jets
Camera Misplaced
Airbus A330-243. Minor damage. Thirty-two minor injuries.
Modified as an air tanker/transport and operated by a private company in support of the U.K. Royal Air Force (RAF), the A330 was en route with nine crewmembers and 189 passengers from RAF Brize Norton in Oxfordshire, England, to Camp Bastion Airfield in Afghanistan the night of Feb. 9, 2014.
The flight progressed without major incident until the aircraft neared the eastern shore of the Black Sea at Flight Level (FL) 330 (approximately 33,000 ft). “The captain (occupying the left-hand flight deck seat) suddenly felt a sensation of weightlessness and being restrained by his harness, accompanied by a rapid pitching down of the aircraft,” said the report by the U.K. Military Aviation Authority (MAA).
The copilot, who had vacated the flight deck for a break and was in the galley when the upset began, was among several occupants “thrown towards the cabin roof” by the negative g forces generated by the sudden dive, the report said.
The captain attempted to regain control by pulling back his sidestick but was able to move the control only slightly aft. He believed at first that the autopilot had malfunctioned.
As the A330 continued the rapid descent, the g forces were such that the copilot had difficulty in re-entering the flight deck. “He reported a disorderly scene with audio alarms sounding and a violent shaking of the aircraft,” the report said.
The MAA determined that the upset was initiated when the left sidestick control was jammed full forward, causing the autopilot to disconnect and the aircraft to pitch nose-down. Investigators found that the captain had been taking photographs with a single-lens-reflex camera while alone on the flight deck. About three minutes before the upset, he had stowed the camera on the shelf aft of the sidestick and forward of the left seat armrest. The captain subsequently moved his seat forward, and the armrest pushed the camera forward against the sidestick, moving it to the full-nose-down position.
During the upset, the A330 descended 4,400 ft within 27 seconds. The descent rate peaked at 15,800 fpm, and indicated airspeed increased to Mach 0.9, or 358 kt. G forces ranged from minus 0.58 g at the onset of the dive to 2.06 g during the recovery.
The report attributed the upset recovery to the A330’s automatic flight control system. As designed, the system moved the elevators to the neutral position when the pitch attitude reached 17 degrees and reduced thrust to idle when airspeed increased beyond 330 kt.
The pilots manually completed the upset recovery, declared an emergency and diverted the flight to Incirlik Air Base in southern Turkey, where the aircraft was landed without further incident.
Twenty-four passengers, six cabin crewmembers and the copilot sustained minor injuries during the upset; and one passenger experienced an acute stress reaction (also classified as a minor injury). Medical personnel aboard the aircraft provided first aid, and the injured occupants later were taken to a base hospital, treated and released.
Examination of the aircraft showed that many interior fixtures had been damaged, but no structural damage was found.
Generator Ground Lug Fails
Boeing 737-300. Minor damage. No injuries.
The 737 was departing from England’s Leeds Bradford Airport the morning of Aug. 2, 2013, when the commander’s primary flight and navigation instruments, the flight management computer and other electrical equipment failed. The copilot’s instruments and the standby instruments continued to function properly.
“There was also a smell of electrical burning in the passenger cabin, so an immediate return to the airport was carried out” in visual meteorological conditions (VMC), said the report by the U.K. Air Accidents Investigation Branch.
Examination of the aircraft revealed that the loss of electrical power was caused by the fatigue failure of a terminal lug that attaches the no. 1 generator’s ground cable to the engine firewall.
“An inspection revealed a number of other lugs which had cracked in the same location, two of which were close to failing in the same manner,” the report said. “The lugs had probably cracked as a result of a combination of engine vibration, a rough surface finish and bending of the lugs during installation.”
Pressurization Malfunction
Boeing 747-400F. No damage. No injuries.
About 25 minutes after departing from Taiwan for a cargo flight to Abu Dhabi, United Arab Emirates, the night of Sept. 8, 2013, the flight crew received a warning that cabin pressure altitude was exceeding limits. The 747 was at FL 300, and the cabin pressure altitude was 10,400 ft — about 3,400 ft higher than normal — and increasing 400 to 500 fpm.
The crew declared an emergency, donned their oxygen masks and initiated an emergency descent to 10,000 ft. They turned back to Taiwan Taoyuan International Airport and landed the freighter without further incident, said the report by the Aviation Safety Council (ASC) of Taiwan.
Examination of the pressurization system revealed that a duct supplying conditioned air to the forward cargo compartment had detached where the duct assembly connects to a check valve. Investigators found that a clamp on the coupling had not been tightened sufficiently by maintenance personnel. The ASC also determined that the aircraft maintenance manual did not include instructions on securing the clamp.
Elevator Trim Jams
Dassault Falcon 20. No damage. No injuries.
While conducting a visual approach to Shreveport, Louisiana, U.S., during a cargo flight the night of Dec. 11, 2014, the copilot found that he was applying more aft pressure than normal on the control column (yoke) after disengaging the autopilot at 2,000 ft.
“The copilot [who was flying from the left seat] stated that below 20 feet AGL [above ground level] and into the landing flare, the yoke hit the aft stop,” said the report by the U.S. National Transportation Safety Board (NTSB). Nevertheless, the crew was able to land the airplane without further incident.
“After landing, the flight crew conducted a post-flight examination, which revealed that the elevator trim was in the full nose-down position and that it could not be returned to the takeoff or neutral position,” the report said. “The flight crew pulled the circuit breaker and used the emergency trim to move the elevator trim to the takeoff position.”
However, after the circuit breaker was reset, the elevator trim moved back to the full nose-down position.
Examination of the Falcon’s elevator trim system revealed that a short circuit in a wire connecting two terminal junctions was causing the elevator to trim full-nose-down despite the position of the trim switch on the left control yoke.
“Further examination also found that the connector at another terminal junction had shorted,” the report said. “The wires and connectors were removed and replaced, and the trim anomaly was resolved.”
Turboprops
Engine Fails on Final
Fairchild Metro III. Destroyed. Five fatalities, one serious injury, one minor injury.
The Metro was en route in VMC to Red Lake, Ontario, Canada, on the third leg of a five-leg scheduled flight the evening of Nov. 10, 2013. There were five passengers aboard, and the flight crew was cleared by air traffic control (ATC) to conduct the VOR/DME (VHF omnidirectional radio/distance measuring equipment) approach to Runway 26 at the uncontrolled airport.
The aircraft was “approximately 500 ft above ground level and approximately 1.4 nm [2.6 km] from the runway [when] the crew noted an aircraft malfunction but did not immediately identify the nature of it,” said the report by the Transportation Safety Board of Canada.
Investigators later determined that the left engine had lost power because a stator vane had been burned through, creating vibration and heat stress that led to the separation of several first-stage turbine vanes. Despite the damage, the engine continued to run but did not provide enough power to drive the propeller.
The only instrument indication of the problem was a slight decrease in left-engine torque. Moreover, the difference in the torque being produced by the left engine and the right engine was not sufficient to activate the Metro’s negative torque sensing (NTS) system, which would have feathered the left propeller automatically if the torque differential had reached about 4.7 percent.
“The right engine was at a low power setting when the left engine power loss occurred, which would have made it difficult for the pilot flying [the captain] to sense the yaw resulting from the malfunctioning engine,” the report said.
Unaware of the nature of the engine malfunction and possibly believing that the NTS would activate in any event of a power loss, the crew did not manually feather the left propeller, the report said. They selected maximum power on “one or both engines” and selected the landing gear up; however, the crew unaccountably reselected the landing gear down before it could fully retract.
“The crew declared an emergency with [a flight service specialist] and unsuccessfully attempted to initiate a climb,” the report said. “Shortly afterwards, the aircraft veered and rolled to the left, descended and struck trees with its left wing. The aircraft continued through the trees and struck a series of hydro lines that ran parallel to [a highway] before coming to rest in a wooded area adjacent to the highway.”
Three passengers and both pilots were killed. The other two passengers were injured but were able to evacuate from the Metro before it was consumed by fire.
Wind Shear Forces Undershoot
Pilatus PC-12/47. Minor damage. No injuries.
The PC-12 encountered moderate turbulence as it neared the airport in Coober Pedy, South Australia, the afternoon of Sept. 23, 2014. The pilot saw blowing dust and virga extending 8,000 ft from the cloud bases at 12,000 ft.
The airport’s wind-reporting equipment was out of service, but the pilot noticed a wind speed indication of 60 kt on the global positioning system display as the aircraft entered the landing pattern.
“The pilot positioned for a landing on Runway 32, which he assessed as the preferred runway given the strength and direction of the wind,” said the report by the Australian Transport Safety Bureau (ATSB). “As he descended through about 500 ft AGL on final approach, the pilot lost visual contact with the runway due to blowing dust and discontinued the approach.”
The pilot said that the runway was clearly visible during the second approach, but the aircraft encountered strong wind shear and turbulence as it descended below 100 ft AGL. “Almost simultaneously, the aircraft was engulfed in what appeared to be a swirling cloud of blowing dust that swept up from beneath the aircraft.”
The aircraft’s sink rate and the turbulence were such that the pilot decided he could not safely conduct another go-around, the report said. The PC-12 touched down short of the runway and came to a stop within 150 m (492 ft). Neither the pilot nor his passenger was hurt.
The pilot initially was not aware that the aircraft had struck the airport perimeter fence during the landing. He examined the aircraft after taxiing it to the ramp but found no damage. After refueling, he continued the flight to Adelaide.
The pilot received an unsafe indication when he extended the landing gear, but all indications were normal after he recycled the gear. After an uneventful landing, a close inspection of the PC-12 revealed minor damage to the nose landing gear bay and to the bottom of the left wing and flap, the report said.
Piston Airplanes
Power Loss Traced to Fuel Servo
Piper Aerostar 601P. Destroyed. One fatality.
Witnesses saw the Aerostar flying low and slowly, with the left engine sputtering and trailing smoke, as it neared Austin-Bergstrom (Texas, U.S.) International Airport the afternoon of Sept. 10, 2014. The airplane then struck trees and crashed in a field about 0.5 nm (0.9 km) from the runway.
Examination of the airplane, which had received a Machen Superstar conversion with intercooled Lycoming IO-540 engines, revealed that the rubber boot connecting the left engine’s intercooler to the fuel injector servo had not been installed properly during an engine overhaul or a periodic inspection, the NTSB report said.
The clamp was loose, and the boot had detached and had been partially ingested by the fuel servo, “which caused an excessively rich fuel-air mixture that would not support combustion,” the report said.
Skydiving Guidance Neglected
Beech G-18S. Destroyed. One fatality.
The airplane was being flown at 100 mph with the flaps retracted as it neared the skydiving drop site near Taylorville, Illinois, U.S., at 11,000 ft the morning of Aug. 11, 2012. The NTSB report said that this was contrary to the operator’s written guidance that airspeed be maintained between 110 and 120 mph, and flaps extended 30 degrees.
Although the operator also recommended that only four parachutists be positioned near the cabin door before a drop, five parachutists were “hanging onto the outside of the airplane, several of the other parachutists were standing in the door, and the remainder of the parachutists were standing in the cabin forward of the door,” the report said, noting that this caused the center of gravity to shift aft.
The Twin Beech stalled, and all 12 parachutists jumped free of the airplane as it rolled and began to descend.
“Several witnesses reported seeing the airplane turning and descending in an inverted nose-down attitude,” the report said. The airplane then entered a nearly vertical dive and crashed in a residential area. The pilot was killed, but no one on the ground was hurt.
Loose Fitting Induces Hypoxia
Reims F406. No damage. No injuries.
The pilot and a navigator departed from Emerald, Queensland, Australia, for an aerial survey mission the morning of Aug. 1, 2014. (The F406 is an unpressurized, twin-turboprop version of the Cessna 404 manufactured in Reims, France.)
The pilot and the navigator, who was operating survey equipment in the passenger cabin, donned oxygen masks as the aircraft climbed above 8,000 ft. The pilot monitored the supplemental oxygen flow as well as his blood oxygen saturation level with a pulse oximeter attached to a finger.
“The pilot recalled that everything appeared normal as the climb continued, but passing about FL 180 he noticed that his blood oxygen saturation level had fallen significantly” to about 77 percent as compared to a normal level of more than 90 percent, the ATSB report said. “Aware that the pilot was experiencing some difficulties with his oxygen supply, the navigator moved forward in the cabin to render assistance and to more closely monitor the actions of the pilot.”
The pilot’s handling of the aircraft deteriorated, and he did not reply to several ATC radio transmissions. He realized that he was losing situational awareness but apparently did not heed the navigator’s recommendations to initiate a descent. The aircraft continued to climb to about 24,500 ft.
“Despite his apparently hypoxic condition, the pilot was ultimately able to identify that an oxygen supply system fitting [beneath his armrest] had become disconnected,” the report said. “When he reconnected the fitting, he took a number of deep breaths and sensed almost immediate relief.”
The pilot initiated a descent, turned back to Emerald and landed the F406 without further incident.
Helicopters
Low Oil Pressure Unheeded
Eurocopter AS-350B2. Substantial damage. One serious injury, three minor injuries.
A witness saw black smoke emanating from the engine exhaust stack as the emergency medical services helicopter departed from a hospital helipad in Ackerman, Mississippi, U.S., to transfer a patient to Jackson the night of Sept. 19, 2013.
About 10 minutes later, the pilot observed the illumination of the low engine oil pressure warning light as well as a low pressure indication on the gauge.
“There was no rise in the oil temperature or the exhaust gas temperature,” the NTSB report said. “Because the pilot had recently experienced an intermittent oil pressure gauge problem in another helicopter, he assumed the accident helicopter was experiencing a similar problem and continued toward the intended destination.”
Several minutes later, the pilot observed a low torque indication and an increase in exhaust gas temperature. He located a suitable landing site, but a total loss of power occurred before the helicopter reached the open field. The patient and the two medical flight crewmembers sustained minor injuries, and the pilot was seriously injured during the subsequent hard autorotative landing.
Investigators determined that when the second-stage turbine wheel was replaced 12 flight hours before the accident, a maintenance technician did not clean the rear bearing in accordance with the manufacturer’s guidance. This “resulted in an obstruction of solidified oil carbon in the rear bearing chip detector housing union, subsequent oil exhaustion and engine failure,” the report said.
The NTSB concluded that the inadequate maintenance was a contributing factor but that the probable cause of the accident was “the pilot’s improper decision to continue flight with a low engine oil pressure warning light instead of landing immediately.”
Rotor Debris Strikes Spectators
Eurocopter EC-120B. Substantial damage. One fatality, two serious injuries, three minor injuries.
The pilot was taxiing the helicopter sideways about 50 cm (20 in) above the ground to perform a demonstration flight during an air show at the Robfeld (Germany) Glider Airfield on Sept. 9, 2012. The helicopter entered a slow descent, and the left landing skid struck the ground.
The helicopter then rolled over, and the main rotor blades fractured. The pilot and his passenger sustained minor injuries. Debris from the rotor blades struck four spectators who were standing about 45 m (148 ft) from the crash site. One of the spectators was killed, two were seriously injured, and the fourth sustained minor injuries.