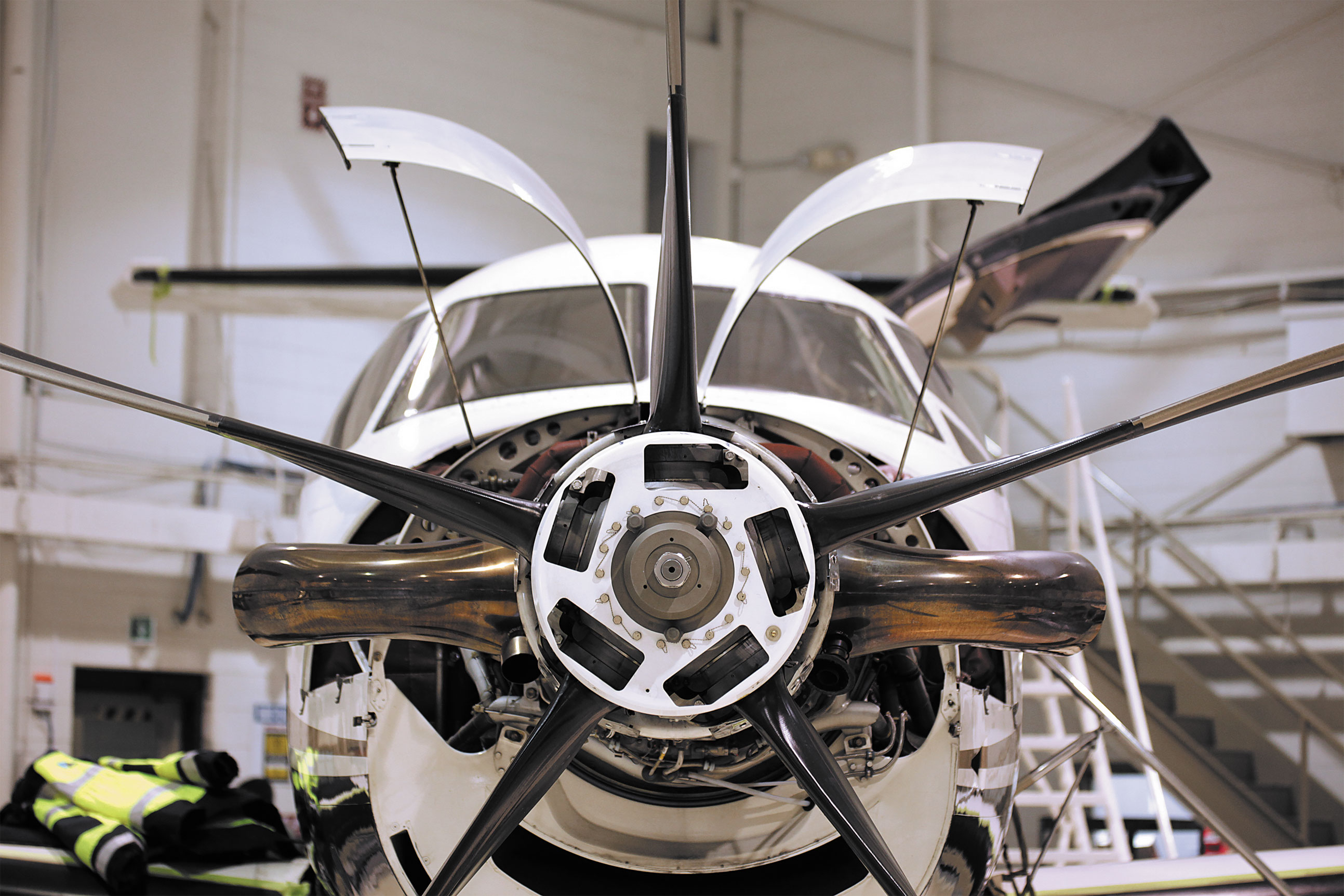
A failure to follow procedures (FFP) plays a part in up to 87 percent of safety events in aviation maintenance, with that number likely to be reduced only through a systematic approach that addresses contributing factors at all levels of a maintenance organization, according to a report by the U.S. Federal Aviation Administration (FAA).1
“Many maintenance-related safety events are the result of employees not following prescribed procedures for completing a task,” said the report, based on a review of several hundred technical reports and other scientific documents regarding factors that contribute to FFP in aviation maintenance and potential mitigations. “FFP refers to situations in which someone, whether intentionally or not, failed to follow a written procedure or policy.”
The FAA’s requirement to comply with instructions exactly as they have been written is “straightforward, but complying with it is not,” according to the report, which was published in January by the FAA Office of Aerospace Medicine. The document added that numerous human factors issues may complicate compliance with written procedures.
As an example, the report cited the Dec. 7, 2011, crash of a Eurocopter AS350 B2 near Las Vegas, Nevada, U.S., that killed the pilot and four passengers and destroyed the helicopter. The U.S. National
Transportation Safety Board (NTSB) found that the crash resulted from failures during maintenance, including “not following self-locking nut reuse guidance/procedures, improper or lack of installation of a split (safety) pin and inadequate post-maintenance inspection.” Contributing factors included fatigue on the part of the mechanic and the post-maintenance inspector, the “lack of clearly delineated maintenance task steps to follow” and the “lack of clearly delineated inspection steps.”2
The NTSB logged the accident as a “maintenance failure,” but the FAA report noted other issues, including the failure of non-maintenance personnel to recognize the errors and the organization’s work scheduling practices.
“Importantly, this example illustrates that FFP events can occur for many reasons within and beyond the control of the front-line employees, showing why it is necessary to intervene at multiple levels within the organization and across the industry,” the report said. “Until systemic mitigations are implemented across the aviation maintenance industry, FFP is likely to remain a high-prevalence challenge with significant human and financial costs.”
Major Challenge
The report described FFP as a major human factors challenge in aviation maintenance, noting that earlier research said FFP contributes to a substantial number of maintenance-related events – various estimates ranged from 40.5 to 87 percent.
Solutions to the problem cannot revolve around “a person-centered approach” that addresses the fitness for duty, training/knowledge and attitude of an individual maintenance workers, the report said. Instead, because FFPs are “an amalgamation of influences from multiple levels of the organization,” solutions must consider the full operational context, the report added.
“That operational context not only contains the individuals performing the work but also factors related to the environmental and working conditions, crew coordination (colleagues and supervision) and the organizational context (culture, resource management),” the report said. “When considering these broader contextual factors, a much more complex and dynamic view of FFP emerges, [leading] to more robust mitigation strategies.”
The vast majority of FFPs are unintentional errors, the report said, adding that about one-third involve inspection errors and a similar number, installation errors.
Earlier research identified specific error types, including attention/memory and perceptual errors, which typically involve failing to detect a defect, forgetting a step in the process, performing a task automatically without paying attention, or distractions and interruptions. Other error types are skill/technique-based errors, knowledge/rule-based errors and judgment/decision-making errors.
Earlier research also estimated that between 16 and 34 percent of FFPs involve willful rules violations, including routine violations, often because an individual believes there is a faster or easier way of doing something; infraction/situational violations such as the inappropriate use of tools, and the less common exceptional/flagrant violations such as falsifying qualifications or signing off work without an inspection.
Although individuals can implement some mitigating actions, their organizations share the responsibility, the report said, citing as an example an individual who implements effective fatigue countermeasures but then is asked by an employer to work back-to-back shifts. Similarly, individuals can try to eliminate stress in their personal lives, but an employer’s action is needed to address workplace stressors such as time pressure and workload.
Employees and employers share responsibility for addressing complacency and lack of assertiveness, both of which can contribute to FFPs, the report said, recommending the use of checklists and the verification of that work has been completed correctly.
Organizational Culture
Overall, the report said, FFPs must be viewed within the broader organizational context in which they occur. Among the organizational contributors to FFPs are organizational culture, pressure and resource management, selection and training, and the quality of technical documentation.
“[W]e advise adopting principles of high-reliability organizations,” the report said, adding that these organizations typically have “informed, reporting, just, learning and safety cultures” and typically experience “fewer adverse events because they recognize humans are fallible and that things can go wrong.”
The document added that organizational cultures can be improved by taking action to “reduce barriers to reporting (fear of blame), encourage honest reporting, assure management commitment and stress the importance of the collection, analysis and sharing of risk-related information within and across organizations/industries.”
Historically, FFP events have been addressed through “a person-centered approach of ‘blaming and training,’” blaming problems on an individual worker’s lack of skill, fitness for duty or knowledge, the report said.
“Although blaming-and-training can be faster and easier in the short term, the scientific literature has found that such person-centered mitigations do not effectively reduce FFP,” the report added. “Instead, a systematic approach is needed where contributors at all levels of the organization are considered and mitigated.”
The report cited a number of actions available to employers to mitigate the conditions that can lead to FFPs, including establishing fatigue risk management systems, reducing employee workload and time pressures, and creating employee well-being programs, which can help reduce physical stressors. Employers also could improve working conditions “that are beyond employee levels of comfort,” such as noise and lighting problems and poorly designed workplaces, the report said.
“Organizations should also strive to reduce pressure (e.g., time, workload) and carefully manage resources in light of constraints like financial viability and an industry shortage of maintenance personnel,” the report said. “Organizations need a robust process for recruitment, selection and training to ensure that employees can maintain and update the necessary [knowledge, skills and abilities] to perform the work. Finally, organizations must ensure the technical documentation is accurate, complete and usable; else it is unlikely to be followed.”
Image: © vectorarts |iStockphoto
Notes
- Key, Kylie N.; Schroeder, David J.; Durham, Justin D.; Choi, Inchul; Hu, Peter T.; Avers, Katrina E. FAA Office of Aerospace Medicine Report No. DOT/FAA/AM-22/01, “Procedural Noncompliance in Aviation Maintenance: A Multi-Level Review of Contributing Factors and Corresponding Mitigations.” January 2022.
- NTSB. Accident Report No. NTSB/AAR-13/01, “Loss of Control; Sundance Helicopters Inc., Eurocopter AS350-B2, N37SH; Near Las Vegas, Nevada; December 7, 2011.” Jan. 29, 2013.