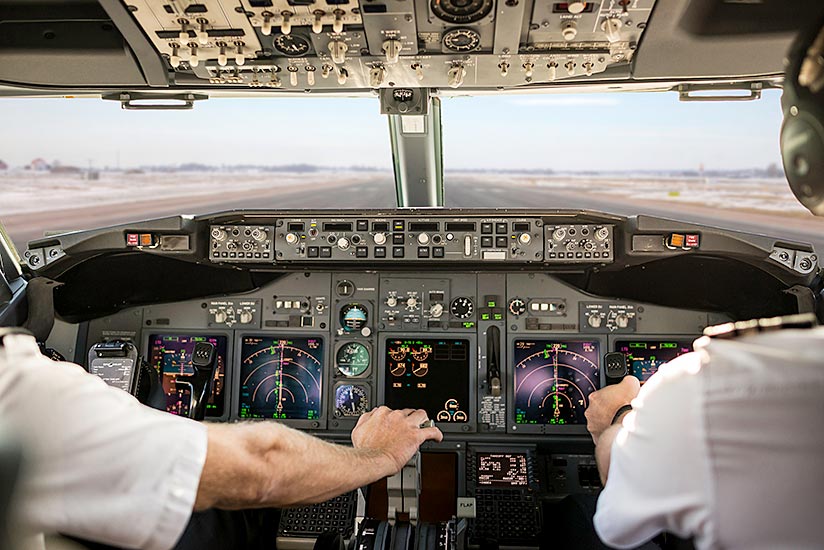
The long list of possible anomalies contributing to unanticipated performance during a takeoff ground run includes engine rollback, stuck brakes, underinflated tires, an unexpected wind vector, non-standard configuration, a contaminated runway, improperly serviced strut oleos, and a host of others, but most cases are just the consequence of pilot input of erroneous data, the decision to take off from an intersection or the selection of the wrong runway entirely.
Regulators and aircraft manufacturers have addressed the issue with technology and more robust procedures, but incidents continue. Why?
What plagues our approach is its philosophy of preemption. Every mitigation measure to date is a variation on the theme of applying a more elaborate system of interlayered checks, in the hope that someone (or something) somewhere will discover inconsistencies in the flow of events leading up to takeoff. The centroid of this approach hinges on the proper practice of cockpit crew coordination and efforts to enhance teamwork. Success is gauged by one’s ability to rigidly adhere to rote procedure, and after the throttles go forward “hope” is the plan.
As the U.S. Federal Aviation Administration (FAA) said in its Pilot Guide to Takeoff Safety,1 a takeoff conducted below field length limit weight (what they call “the most likely takeoff scenario”) is: “possibly the most easily misunderstood area of takeoff performance, since the fact that the aircraft is not at a limit weight is about all the flight crew can determine from the data usually available on the flight deck. Currently, few operators provide any information that will let the crew determine how much excess runway is available; what it means in terms of the V1 [defined by the FAA in part as “the maximum speed in the takeoff at which the pilot must take the first action (e.g., apply brakes, reduce thrust, deploy speed brakes) to stop the airplane within the accelerate-stop distance”] speed they are using; or how to best maximize the potential safety margins represented by the excess runway.”
No effort has yet been invested in enabling the flight crew to detect (and react to) inconsistencies early during the actual ground run. The first opportunity they are afforded to address a condition that might be amiss is when they try to rotate and discover they are now tailwheel rated in tricycle airplanes.
The solution put forward in the following paragraphs assumes there is no operational need to repetitively try to reverify VMU speed (minimum unstick speed, or the speed at which an airplane can safely lift off), and instead attempts to illustrate one potential method to eradicate this trend from further incident reports.
The speed tapes on the left edges of the primary flight displays (PFDs) of both Airbus and Boeing aircraft show calculated values for selected takeoff speeds (Figure 1).
The conventional speed tape is somewhat disarming for the first-time user because during acceleration it is always “descending,” which can be counterintuitive knowing aircraft speed during this time should be increasing. More importantly, the speed tape offers the pilot no indication of whether the aircraft is accelerating in accordance with preflight flight management computer (FMC) calculations. It gives a linear readout of the one-dimensional parameter of dynamic air pressure and is used by the pilot on takeoff for no other purpose than to time the application of nose-up stick input.
Also absent from the modern speed tape is information about how much distance is consumed in the attainment of any airspeed, how much physical runway is remaining, or how either of those measure up to expected performance. A check that both navigation displays are coincident with runway heading and an “80 knots” or “100 knots” callout is traditionally made, but what is being done from brake-release to the moment the flight crew attempts to rotate? Is there any better time than this to ensure proper aircraft acceleration on behalf of the decision to reject takeoff safely in the low speed regime? What if there was a reliable way to detect a discrepancy between calculated and actual takeoff performance within the first 500 m (1,641 ft) of ground?
Imagine for a moment that you are the first officer and the pilot flying on an aircraft that you have just lined up on runway centerline for takeoff. Landing traffic has vacated, you are cleared for takeoff, the assumed temperature is set, the brakes are released, groundspeed is alive, and things are go. Imagine also that you fly for a carrier that had the foresight to add the take-off performance indicator (TOPI) to the PFDs and head-up displays (HUDs) of its fleet, and that the TOPI takes the place of the traditional speed tape for the duration of takeoff from the moment it is “armed” until the weight on wheels microswitches confirm main gear liftoff.
You glance down to crosscheck your TOPI (Figure 2) and see that you have over 9,000 ft (2,745 m) of actual runway remaining in front of you and that the projected stopping line for a rejected takeoff (RTO) at V1 (horizontal white line) is well within that. You note how the expected performance carrot, or EPC (green chevron), is tracking with current airspeed (50 kcas), and that this confirms that aircraft acceleration (the constantly updated ratio of aircraft groundspeed to distance traveled) is within the tolerances of the FMC. Your training has prepared you to react properly to the two possible ways this might progress. Current airspeed, for whatever reason, might lag the EPC, in which case the TOPI would eventually develop into a degraded performance condition that looks like Figure 3.
This would trigger an alarm enabling you to decide whether to reject the takeoff early, while still well within the low speed regime.
Or, current airspeed might lead the EPC, in which case you would know that aircraft acceleration, for whatever reason, exceeds calculations, and the TOPI would develop into a condition like Figure 4.
This situation, while not adverse, is clearly indicative of some kind of anomaly, and while an alert would be triggered, the decision to reject the takeoff is still up to you and the captain. The key here is that a TOPI would allow both of you as a flight crew to make such a decision well before you encounter the risk of a high-speed rejection of the takeoff.
Assume for a moment that gross weight and center of gravity entry went well, wind is as forecast, and the aircraft is not suffering from any unknown anomalies. In this case, acceleration is on schedule down the correct runway in the correct direction, and the TOPI has tracked upward to abeam V1 (Figure 5):
With slightly more than 3,000 ft (915 m) of runway remaining, you get the V1 callout, and see that an RTO at this speed would still have extra runway available — as indicated by the gap between the white RTO stop and actual runway remaining lines.
The EPC is an indication of the expected ratio of groundspeed to distance travelled, as per initial FMC data entry. The current airspeed line, while of course displaying the current airspeed, moves as a global positioning system (GPS)-derived real-time indication of the actual ratio of groundspeed to distance travelled and is positioned in lag or lead relative to the EPC to indicate either a deficiency or excess measure of acceleration.
TOPI logic would enable the EPC, V1, Vr, current airspeed line, and the RTO stop line indications (although initially positioned prior to pushback based on FMC entry of anticipated wind) to be dynamically adjusted with the real-time runway wind component during the takeoff ground run. This means that the wind component down the runway (the difference between KCAS and groundspeed at any given moment) would be applied as soon as groundspeed is alive and the minimum KCAS sensing threshold is met. The TOPI indications would always reflect the actual wind vector.
In a situation of large/rapid runway wind component fluctuations (shear), the EPC will therefore be seen to move either slightly up or down as these are sensed. The aircraft current airspeed line (shown just to the left of the EPC) will also undergo the same movements in response to the same changes in prevailing wind component.
So, in any takeoff situation where wind shear is expected to be a factor, the pilots would brief this issue when discussing the weather, and expect a certain degree of slight TOPI “surge,” knowing that it is just a reflection of wind component fluctuations, and not a reflection of any acceleration performance anomalies.
An engine rollback, engine failure, manual reduction of thrust lever position, or any other rapid deceleration during a takeoff ground run will be immediately apparent from the downward movement of the current airspeed line as well as the upward movement of the V1, Vr (rotation speed) and the RTO stop lines to their new positions farther down the runway.
The hardware required to incorporate the TOPI into the PFDs and HUDs of modern airliners already exists on the vast majority of aircraft, and the algorithms necessary to calculate dynamic values for the EPC, V1, Vr and the RTO stop line are active pieces of operational FMC software or were already established during certification flight tests.
Let’s look at a few instances of takeoff performance anomalies in recent years and examine how (if at all) things would have transpired differently had the aircraft been equipped with a TOPI.
A US Airways Airbus A320 was entering Philadelphia International Airport’s Runway 27L in March 2014 for takeoff when the crew discovered the flight management system had been initialized with a FLEX takeoff from Runway 27R, a runway of different length. The new runway was quickly entered, but a new FLEX temperature and V-speeds were not uploaded. The crew, however, commenced takeoff without any V-speeds on the speed tape. Callouts were therefore impossible, and conditions during the ground run told the aircraft that it was about to land — as indicated by the aural command to “retard.” Despite this, the captain elected not to execute an RTO until after attempting to rotate, at which time the aircraft was already well over V1 speed. Trying to slow the aircraft in these conditions eventually put it off in the grass to the left of Runway 27L.
Had this A320 been equipped with a TOPI, the first thing the crew would have noticed after the entry of the new runway without the new FLEX temperature would have been a red “X” denoting that no V-speeds and no RTO line had been calculated (Figure 6).
The lack of any performance information (to include the absence of current airspeed) would have been obvious to both crewmembers and would likely have discouraged them from initiating takeoff until properly configuring the performance data.
In another occurrence, a Jet Airways Boeing 777-300 fully loaded with passengers and fuel for a flight to Mumbai was taxiing for departure at London Heathrow Airport in August 2016. The crew selected a V1 based on a derated thrust setting requiring 11,000 ft (3,355 m) of runway, but then proceeded to commence the takeoff from intersection S4, from which only 7,715 ft (2,353 m) were available. The aircraft finally became airborne with slightly more than 300 ft (92 m) of actual runway remaining, crossing the upwind threshold at 13 ft above the ground.
Had this 777 been equipped with a TOPI, when pulling onto the runway at S4, the flight crew would likely have noticed that the RTO stop line was positioned beyond the actual runway remaining line, outlined and blinking in red — signifying a lack of sufficient runway available to reject the takeoff at V1 (Figure 7).
They would have also likely noticed that V1 and Vr were positioned near the actual runway remaining line, signifying the unusually slim margins available to affect the takeoff.
In March 2018, an El Al 787-9 was climbing out of Tel Aviv on its way to Newark, New Jersey, U.S., when the flight crew noticed the display of an unusually high initial cruise altitude for (what they thought had been entered as) aircraft weight. A subsequent check of preflight performance calculations revealed that a zero fuel weight 40 tons lower than actual had been used, and that the aircraft, unbeknownst to the crew, had managed to get airborne right around stall speed. A derated thrust setting for the erroneous weight was in use throughout the 13 seconds from rotation until the 787 reached 35 ft above ground level. The aircraft had gotten airborne 80,000 lb (36,288 kg) heavier than expected because the tail strike protection logic automatically limited the pilot’s rotation input.
Had this new 787 been equipped with a TOPI, the first indication the flight crew would have had suggesting the existence of some anomaly would have been the discrepancy between the current airspeed line and the EPC (Figure 8).
This discrepancy would have likely cued them in early to the fact that the aircraft was not accelerating as calculated, and that this could be due to the mistaken entry of takeoff data. The TOPI, though, is not a feature designed to do the thinking for a flight crew, and the decision regarding whether to reject a takeoff is still in their hands.
The TOPI is a conceptual adaptation of what others may know as the line speed check — the process of confirming aircraft acceleration as early as possible in the takeoff. The technique is primarily confined to the operation of single engine aircraft due to the seriousness of losing the only available source of propulsion, but it also has broad potential for application in the transport category.
Editor’s Note: The opinions expressed are those of the author and not necessarily of Flight Safety Foundation.
Mark Jones is a U.S. Merchant Marine Academy graduate with military and civilian flight experience. He is passionate about bringing new thinking to old issues of cockpit design.
Note
- FAA. Pilot Guide to Takeoff Safety. October 2011.
Featured image: © MatusDuda | iStockphoto
Flight display images: Mark Jones